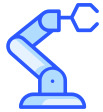
Manufacturing
Manufacturing
Lack of quality control on manufacturing lines
Higher operational costs due to lower levels of automation
Siloed data leads to ongoing operational inefficiencies
Inability to move towards autonomous plants
Supercharging Industry 4.0
Improve asset availability through forecasting early fault detection in critical components and conducting proactive replacements.
Note:
AI – Artificial Intelligence
ML – Machine Learning
MV – Machine Vision
SME – Subject Matter Expert
P&ID - Piping and Instruments Diagram
GHG - Greenhouse Gas
IT - Information Technology
OPAF - Open Process Automation Forum
OT - Operational Technology
0123456789
Decisions will be increasingly made directly on the basis of the AI outcome, starting with low-risk decisions and evolving over time to high-risk decisions.
Note:
AI – Artificial Intelligence
ML – Machine Learning
MV – Machine Vision
SME – Subject Matter Expert
P&ID - Piping and Instruments Diagram
GHG - Greenhouse Gas
IT - Information Technology
OPAF - Open Process Automation Forum
OT - Operational Technology
0123456789
Relevant, real-time data sources are aligned in enterprise data storage to enable accurate and timely AI based decision-making.
Note:
AI – Artificial Intelligence
ML – Machine Learning
MV – Machine Vision
SME – Subject Matter Expert
P&ID - Piping and Instruments Diagram
GHG - Greenhouse Gas
IT - Information Technology
OPAF - Open Process Automation Forum
OT - Operational Technology
0123456789
Maximise usage of 5G-enabled robotics in various parts within manufacturing lines, data collection for remote monitoring, maintenance, etc.
Note:
AI – Artificial Intelligence
ML – Machine Learning
MV – Machine Vision
SME – Subject Matter Expert
P&ID - Piping and Instruments Diagram
GHG - Greenhouse Gas
IT - Information Technology
OPAF - Open Process Automation Forum
OT - Operational Technology
0123456789
Automated quality control employing machine learning with sensors collecting data and alerting during abnormal production for improvement purposes.
Note:
AI – Artificial Intelligence
ML – Machine Learning
MV – Machine Vision
SME – Subject Matter Expert
P&ID - Piping and Instruments Diagram
GHG - Greenhouse Gas
IT - Information Technology
OPAF - Open Process Automation Forum
OT - Operational Technology
0123456789
With 5G-enabled sensors monitoring behavior around the plant to track, manage and predict potential occupational hazards in real-time.
Note:
AI – Artificial Intelligence
ML – Machine Learning
MV – Machine Vision
SME – Subject Matter Expert
P&ID - Piping and Instruments Diagram
GHG - Greenhouse Gas
IT - Information Technology
OPAF - Open Process Automation Forum
OT - Operational Technology
0123456789
Autonomous robots and aerial drones can traverse harsh and dangerous environments and reduce hazard risks for human workers. Such technology will provide enhanced monitoring and safety upkeep for facilities. They can be fitted with various sensors geared towards the purpose they are meant for and by using 5G, we can deploy them in real-time whereby the data collected can be sent directly to an AI application for investigation and immediate further action.
Wearable technology allows security and medical personnel to conduct background and health checks efficiently. Of course, they have a much broader focus and can be used in many different industries where clothing has been enriched with wearable technologies. Wearables are also able to collect extra information for a 5G-enabled digital service.
Sensors are crucial for capturing real-time data and insights and pave the way for more informed decision-making. Sensors will be the data collection point for every 5G-enabled digital service and therefore will have to cover a broad spectrum of types of information to be collected and the way they are connected to the DNB 5G network.
XR is set to take work and play to the next level with cutting edge technology never seen before. These devices have the potential to boost productivity and enhance entertainment, changing the way we experience our reality through digital transformation. There is an increasing broad spectrum of devices available for both consumer and enterprise markets, making it increasingly important for each user experience.
All information provided on potential 5G-enabled solutions and potential vendors is provided for information purposes only and based on our awareness of the available 5G-enabled solutions and potential vendors in the market. It does not constitute endorsement, recommendation or favouring by DNB. It is your responsibility to verify and evaluate such 5G-enabled solutions and potential vendors. DNB is not an agent or legal representative of any of such 5G-enabled solutions and potential vendors, is not associated or endorsed by such potential vendors, has no authority to act on behalf of any such potential vendors, and will be an independent party if you enter a business relationship with such potential vendors. Third party links included are for convenience only and are not under DNB’s control. DNB does not assume any responsibility or liability for your use of such third-party links.